Dayton, OH (August 2023) – Yaskawa America, Inc. will showcase advanced robotic automation solutions created to positively impact manufacturers of all sizes at FABTECH, September 11-14 in Chicago, booth #B20051.
Experts from the Motoman Robotics Division and the Drives & Motion Division will be present to discuss specific application requirements. “Our featured robots and workcells showcase a wide range of welding expertise,” offers Josh Leath, Sr. Product Manager of Welding for Yaskawa Motoman. “The advanced technologies on display are proven to help increase quality, safety and throughput for manufacturers in a wide range of industries, and our ability to provide custom solutions can also assist complex tasks for improved operations.”
The Yaskawa booth will feature the following demonstrations:
Welding
Yaskawa’s Most Compact Welding Workcell
Ideal for supplementing or replacing manual, small part welding, the extremely compact and flexible ArcWorld® HS is a space-saving solution for tight production layouts. Requiring only 1.4 square meters (15 sq ft) of floorspace, this model utilizes a six-axis AR900 arc welding robot and has a hinged station (HS) door, allowing easy access for loading and unloading parts. This workcell also highlights Yaskawa’s Universal Weldcom Interface (UWI) pendant application that helps users gain easy control of any weld process or parameter.
Portable Collaborative Welding Workcell
Part of Yaskawa’s proven line of ArcWorld workcells, the ArcWorld HC is a portable job shop that facilitates human-collaborative (HC) interaction. Specifically designed for optimizing small- to medium-sized part production for medium volume runs, this flexible solution with perforated Flextur™ table comes pre-engineered with arc flash protection, provisions for fume mitigation and an IP67-rated HC10DTP cobot for use in harsh welding environments. An integrated weld package with a Fronius power supply is shown, but all major brands are compatible. This demonstration also highlights the UWI pendant application on standard and smart pendants.
High-Volume Welding Workcell
Built for high robot utilization, the ArcWorld 6200 is ideal for medium- to large-sized parts or high quantity production runs. Featuring two streamlined AR1440 robots with expanded wrist range for improved flexibility, multiple robot control with coordinated motion between devices is demonstrated from a single teach pendant. The AC servo-driven RM2-1275 Ferris-wheel positioner included in this demonstration uses the patented MotoMount™ fixture mounting system that allows simple setup, eliminating the need for precision alignment or expensive base plate for simplified tool changeover. ServoRobot seam tracking sensors on both robots allows for adaptive welding to compensate for path or gap variations. Safety fencing by WireCrafters is shown.
Economic and Flexible Welding Workcell
An ideal first step into robotic welding for job shop environments, the ArcWorld LC (LiteCell) is well-suited for mitigating labor shortages and quality concerns. Featuring the pre-engineered safety and efficiency of traditional ArcWorlds, this system is designed to help ensure quick payback for ultimate ROI. Fast and simple to install and relocate, a single power source and Wandelbots ease-of-use programming technology will also be on display.
Hands-on Collaborative Mobile Workstation
Extremely cost-effective for collaborative robot integration, the HC10 Workstation on display features a hand-guided HC10DTP robot. Compatible with Yaskawa’s HC10, HC10DT, HC10XP and HC10DTP collaborative robots, this highly compact solution with internal cable management is easily set up and relocated to quickly add automation to existing production environments. Built-in leveling feet facilitate the utmost stability when the robot runs at maximum speed and payload capacity.
Spot Welding
Automotive Spot Welding Demonstration
Featuring a compact servo-controlled spot gun and a Nadex® DC spot timer, the low-profile SP80 spot welding robot with Tecna Light X-Gun is featured alongside a high payload hollow-arm SP225H robot with a CenterLine FlexGun™ spot gun. Each robot in this demonstration features exceptionally fast axis speeds and acceleration capabilities for reduced air-cut time. Adding greater programming flexibility, the SP225H robot is using an integrated spot harness in the hollow arm. This serves to reduce interference and harness wear, while accommodating a high-density robot layout. A multi-axis, tilt-rotate, low-profile MotoPos 500 positioner expertly presents the part for welding. Overall, this demonstration highlights multiple robot control with coordinated motion between different devices and processes through a single YRC1000 teach pendant for the fabrication of a single part.
Offline Programming
MotoSim EG-VRC Kiosk
Using an extensive model library and many built-in functions, the MotoSim® EG-VRC simulation tool can drastically reduce the time, risk and expense of creating robot jobs and setting up workcell configurations. A PC-based software tool, this extremely accurate Yaskawa robot tool is specifically designed to enable offline programming and help conceptualize all the possible robot scenarios.
Motion Control
Mechatronic Product Kiosk
Offering a comprehensive suite of products, including industrial servo components, machine controllers and HMIs, our sister division (Yaskawa America, Inc. – Drives & Motion), will display award-winning Sigma 7 servo products, including Sigma Trac II linear stage, direct drive rotary motors, gear motors and a hybrid-ready machine controller MP3300IEC, providing up to 62 axes of motion.
3D Printer Demo Optimized for Speed
In this demonstration, a strong, rigid framework and Yaskawa servo control combine to deliver 3D printing at 350 millimeters/sec., setting a dramatically higher standard for additive manufacturing speed with constant precision. A Yaskawa MP3300iec machine controller achieves this productivity with standard G-code, utilization of pre-canned tools such as extruder advance pressure controller, and bed leveling surface compensation couple with a Yaskawa Compass GUI for easy customizing of user controls.
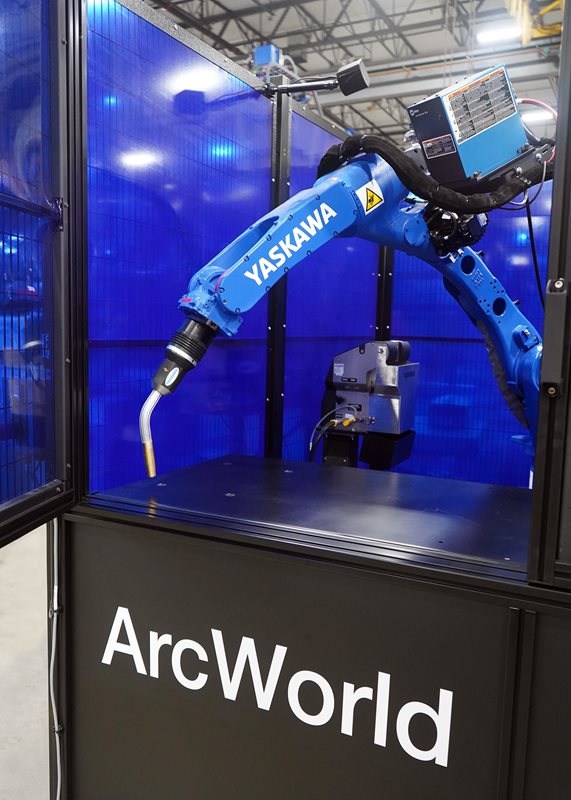